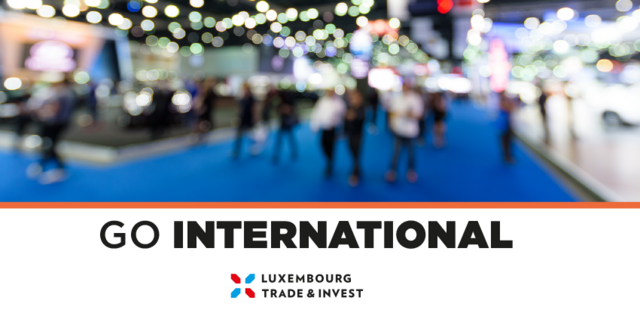

Founded in 1937, Ampacet Corporation is a leading global masterbatch supplier committed to designing innovative, custom colour, special effect, high performance and sustainable products and solutions. Ampacet also manufactures a proprietary line of machinery and feeders for the plastic industry aimed to improve efficiencies in plastics manufacturing.
(Visited 18 March 2022).
Ampacet Europe houses on its Luxembourg site one of the European factories of the group, an R&D laboratory as well as a conception and design centre. Since arriving in the Grand Duchy in 1995, first in Windhof and then in Dudelange, Ampacet has seen continuous growth. The company has already invested more than EUR 40 million in Luxembourg, by setting up, twice, new production lines in Dudelange and installing its European distribution centre within the Eurohub South logistics park (in Bettembourg/Dudelange). Ampacet’s speciality formulations can be found in products in the automotive, housewares, personal care, phamaceutical and medical, sporting goods, agricultural, and many other markets. Headquartered in Tarrytown, N.Y., Ampacet employs more than 2,000 people worldwide, with 26 manufacturing sites including technical and colour development centres in 19 countries throughout the Americas, Asia and Europe. Ampacet Europe currently employs 526 people, including 211 in Dudelange, Luxembourg.
Interview with Marcello Bergamo, Ampacet Europe Managing Director.
What projects are you currently working on?
On a sustainability level, Ampacet has been, is currently, and will continue to be, proactive with its sustainable masterbatch solutions for environmental and societal concerns. With ‘Environmental Care’ as one Ampacet core value, the Ampacet R3 sustainability programme represents the company’s global commitment to sustainable development, offering a growing portfolio of innovative masterbatches benefiting customers, the industry, and the planet.
Ampacet R3 masterbatch solutions support customers in achieving their sustainability objectives and voluntary commitments through improved product designs for the circular economy, the use of optimizsed content from post-consumer recycled material, reduction of fossil-based raw materials consumption, and adoption of alternative end-of-life scenarios.
Ampacet is also investing heavily in projects related to the medical and pharmaceutical markets. Those investments are aimed to support a society driven by changes like an ageing population, dietary changes, development of home healthcare, the COVID-19 pandemic, as well as the increased usage of sterilised and disposable accessories for safety. Plastics have become vital and essential in the medical market as they are replacing conventional materials such as metal, ceramic and glass for their mechanical properties, ease of processing, quality, durability, cost-effectiveness, lightweight features, and ability to take on complex shapes as well as being easy to sterilise.
Ampacet’s unique knowledge and skill set in the use of materials gathered from multiple industries combined with the know-how of its regulatory experts, has led to a portfolio of masterbatch solutions that have been specifically designed for the medical and pharmaceutical markets. The Ampacet ProVital range meets high industry requirements and is compliant with stringent medical regulations.
What achievements are you particularly proud of?
We are very proud of the success of our RECNIR-BLACK product range that has been named a Plastic Recycling Awards Europe winner in the category of Product Technology Innovation of the Year. While most black packaging cannot be sorted by recycling companies and can only be disposed of in a landfill or used for energy recovery, packaging using Ampacet’s REC-NIR-BLACK carbon black-free masterbatch is near-infrared (NIR) transparent to allow scanning by NIR technology for automated sorting at recovery facilities. We are also proud of the way we managed the COVID-19 crisis by being able to respond to a strong demand for the essential products that we manufacture for the health and hygiene industries. The Ampacet team demonstrated the highest level of ingenuity, resilience and tenacity during this complex period.
When was the last time you had a doubt?
Being able to continue serving the vital markets such as pharma and medical, hygiene, food industry and baby care during the COVID-19 crisis, despite employees on sick leave, raw material shortages, transport constraints and other force majeure. Our production planning was overloaded. We ran 24 hours a day, 7 days a week. We even had to establish a priority list to be sure to satisfy customers serving critical markets.
What does it mean for you to have an entrepreneurial spirit?
Having and feeling the responsibility of the company, the business, and the employees to ensure they all have a future, a better future. To me, this is the approach a manager should have and adopt to maintain and prolong the business-life of a company. How to do that? By having an ethical and moral approach towards employees, customers, suppliers. To all business parties, treating them as you would like to be treated. In other words, being fair. It is also being coherent with the business approach, decisions, and way to manage it and anticipating the market changes, thinking strategically on mega-trends, which help position the business for future demands.
Did the COVID crisis have an impact on your business and what do you think the Chamber of Commerce could do to support you?
As mentioned previously, COVID-19 put a strain on our business, increasing the demand of our products. From a staff perspective, like any other company, we had to face absences due to sickness, but we managed this in a way that allowed us to reduce the impact on both production and service. Our business was/is considered an essential business as we provide the base-materials for the pharma, medical and food industries. We have been committed to prevent the interruption or breaking up the supply chain, by prioritising those segments and keeping the production running. As Ampacet operates internationally, the Chamber of Commerce can support the digitalisation process by automating the import/export activities that require certification and/or legalisation of the invoices through the embassy or consulate of the exporting country. Ampacet currently uses the digital platform from the Belgium Chamber of Commerce that provides this service, which connects Ampacet, the Chamber of Commerce and the Embassy.
PHOTOS Laurent Antonelli / Agence Blitz