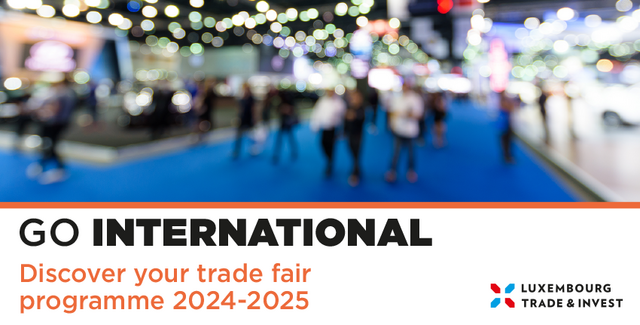
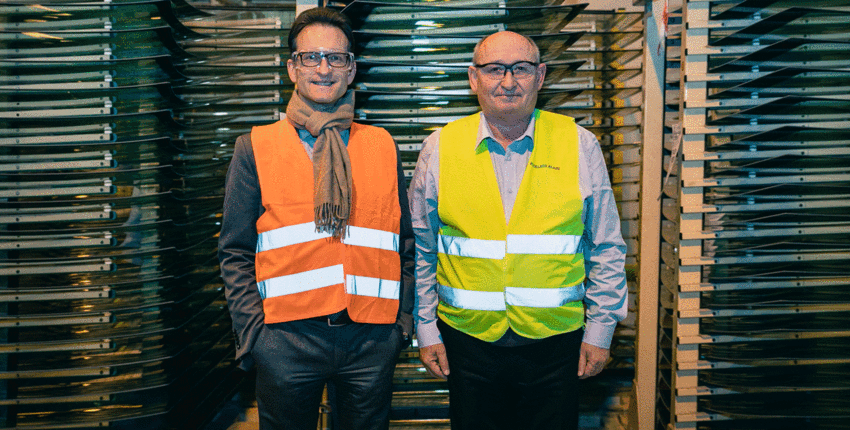
Les origines de Carlex remontent à 1989, lorsqu'un partenariat est établi entre Central Glass Co. Ltd et Ford Motor Co. En 1991, Carlex ouvre sa première usine de verre automobile à Vonore (Etats Unis). En 1995, Carlex Glass Company devient complètement la propriété de Central Glass Co. Ltd, avec ses quartiers généraux basé à Nashville (Etats Unis).
La marque Carlex se concentre alors sur un objectif: fournir les meilleurs produits de verre automobile à ses clients dans le monde entier. Le groupe Central Glass, dont le siège se trouve à Tokyo, possède 10 sites de fabrication de vitres automobiles aux États-Unis, en Europe et en Asie. Le groupe Central Glass est actif dans un large éventail de domaines, notamment le verre architectural, le verre pour l'électronique, les produits chimiques, les engrais, la chimie fine, les fibres de verre et les produits en verre pour automobiles.
En 2014, Carlex a repris les sites de production de verre automobile du fabricant de verre américain Guardian, dont faisait partie l'usine de Potaschbierg et fabrique des produits en verre de qualité supérieure pour les véhicules premium, essentiellement pour le compte des fabricants d'équipement.
Le site de Grevenmacher, grâce à sa position stratégique au cœur de l'Europe, offre ainsi des voies de livraison idéales à d'importants clients européens sur le marché du haut de gamme, notamment Volkswagen (avec des sites de production en Allemagne et en Slovaquie), BMW, Mercedes-Benz, Porsche (Allemagne), Audi (Allemagne, Belgique, Hongrie, Slovaquie), Lamborghini (Italie), Bentley, Rolls-Royce, Land-Rover et Jaguar (Royaume-Uni), Skoda (Hongrie), Chrysler (États-Unis) et Peugeot (France).
En 2018, confirmant son ancrage local, Carlex Glass Luxembourg inaugure une nouvelle ligne de production. La Laminating Line 5 remplace partiellement les anciennes chaînes de production construites en 1992, qui ne répondent plus de manière optimale aux exigences actuelles. Représentant un investissement de près de 25 millions d'euros, la construction de cette nouvelle ligne de production de pare-brises a permis à l'entreprise d'agrandir son site d'environ 3 400 m2, entrepôts compris, occupant une surface globale de 50.000 m2. Carlex Glass Luxembourg emploie actuellement près de 600 collaborateurs et sa production fonctionne 24 h/24 et 365 jours /an.
Entretien avec Alain Roselaer, Plant Manager.
Quels sont les projets sur lesquels vous travaillez actuellement ?
Tous les grands constructeurs automobiles travaillent actuellement sur des concepts de voitures autonomes et électriques avec tout ce que cela comporte de technologies et d'innovations en matière de design automobile et de géométrie des véhicules. Ce nombre impressionnant de nouveautés technologiques intégré aux pare-brises impacte notre métier. Nous y réfléchissons déjà. Puis, en interne, un gros projet sur lequel nous travaillons est la restructuration totale de nos unités de production. Désormais, nous sommes limités dans notre expansion, nous occupons entièrement la surface de notre site. Il nous faut donc optimiser nos espaces de production et de stockage et revoir notre logistique interne.
Quelle est la réalisation dont vous êtes le plus fier ?
Sans aucun doute la Laminating Line 5. Dans un environnement industriel de plus en plus concurrentiel, l'objectif prioritaire de cet important investissement était d'assurer de manière encore plus efficace la satisfaction des acheteurs de l'industrie automobile qui se montrent toujours plus exigeants en termes de réalisations " sur-mesure ", de forme et de qualité des parebrises. Alors que les parebrises préalablement coupés et façonnés à partir de plaques de verre rectangulaires étaient jusqu'à présent chauffés à 600 °C au moyen de la technique dite de " bombage par gravité ", puis pressés pour obtenir la forme désirée, la nouvelle Laminating Line 5 fonctionne selon une tout autre procédé : le système " External Press Bending " qui s'avère être nettement plus efficace. De plus, associée à une réduction des rebuts de production, cette meilleure efficacité énergétique permet à l'entreprise de réaliser de réelles économies. Cette ligne nous permet ainsi de suivre les perpétuelles évolutions du marché.
Quels sont les grands défis auxquels vous devez faire face dans votre secteur d'activité ?
Il y a d'abord à court terme les variations du marché dues à plusieurs facteurs, et nous ne savons pas comment cela va évoluer. Si les constructeurs vendent moins, nous produirons moins et il nous faudra faire des choix pour nous adapter, voire réadapter notre activité. Puis, personne ne sait à ce jour, quel sera l'impact du Brexit sur le marché mondial de l'automobile, comment vont réagir les marchés chinois et américain, qui deviennent par ailleurs, de plus en plus protectionnistes. Enfin, notre plus grand challenge sera de réussir à adapter notre entreprise à toutes les normes et restructurations qui se profilent.
Si vous pouviez changer une chose dans votre secteur d'activité, quelle serait-elle ? Que pourrait faire la Chambre de Commerce en ce sens ?
J'ai un vœu pieux, mais je doute qu'il se réalise. Pour toutes les entreprises comme la nôtre qui dépendent fortement de leurs clients, un peu plus de transparence et de communication seraient les bienvenues. Nos clients sont des donneurs d'ordre et lorsqu'il y a des perturbations sur le secteur de l'automobile, les répercussions ont un effet boule de neige et les problèmes rejaillissent sur toutes les entreprises qui alimentent le secteur. Nous sommes souvent mis devant le fait accompli. Nous devons alors nous adapter et trouver des solutions rapidement au lieu de pouvoir anticiper les transformations. Et nous ne bénéficions pas toujours de l'aide de nos clients pour nous adapter.
Texte: Corinne Briault - Photos: Pierre Guersing